History of Gundrilling
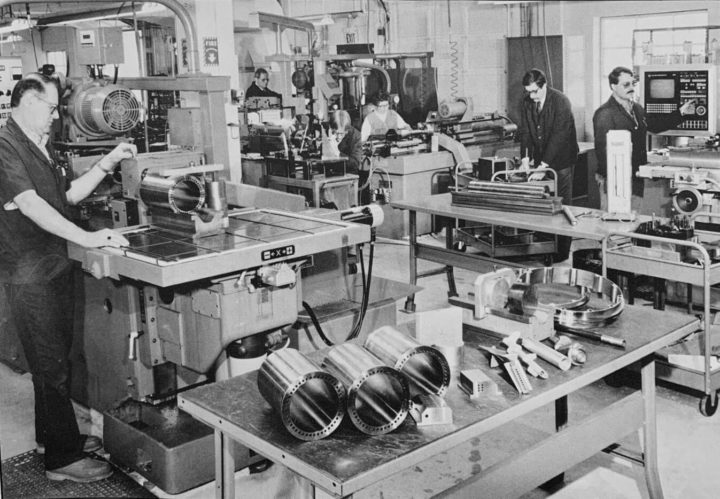
Gundrilling has its roots in Europe during the late 19th- and early 20th-century. Early gun barrels were produced either by roll-forging or “Damascus” spiral welding. The advent of more powerful propellants led to the need for stronger, more dependable steel barrels. Drilling of alloyed steel bars proved necessary.
Drilling with twist drills welded to extended shafts was laborious, time consuming and liable to drift and wander.
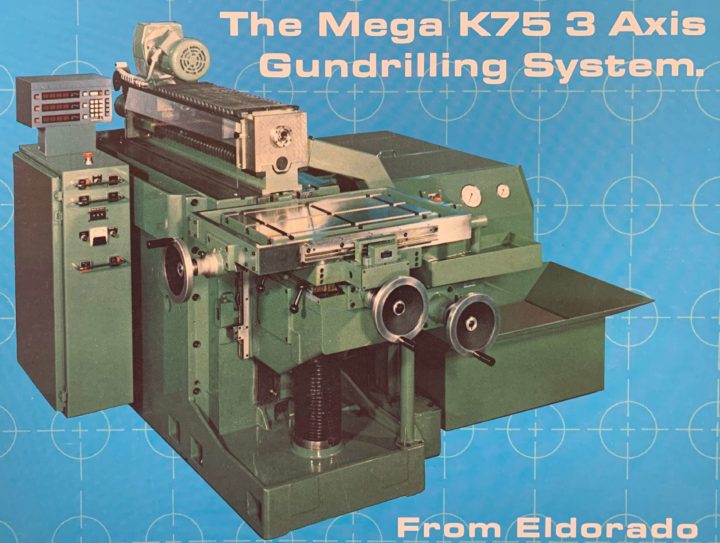
There were already well-established methods used in woodworking for the drilling of deep holes that employed long, straight grooved or D section augers. Such tools, ground with eccentric cutting edges, had been found to provide very straight, controlled results. The successful introduction of these ideas to the cutting of metal greatly improved hole quality.
The final step to bring the gun drill to today’s design occurred in the 1930s with the idea of attaching the cutting tip to a formed tubular shank through which cutting oil could be passed. In turn this flowed through an adjoining hole in the tip to lubricate, cool and flush chips.
Gundrilling today
Modern gundrilling, also known as precision hole drilling, is a single machining technique for drilling holes in metals. The process uses a single lip cutting tool through which cutting oil is pumped under high pressure.
The majority of precision hole drilling machines built today rotate and feed the cutting tool into the stationary workpiece. With a properly designed machine and cutting tool, it’s possible to precision-drill holes with depth-to-diameter ratios of 100:1, 200:1, and even 300:1.
Precision hole drilling offers many advantages, some of which are unattainable with any other machining technique. These advantages are:
- Straightness, Drift, and Depth of Hole
- Close Tolerance of Hole
- Surface Finish
- Productivity
- Unique Capabilities
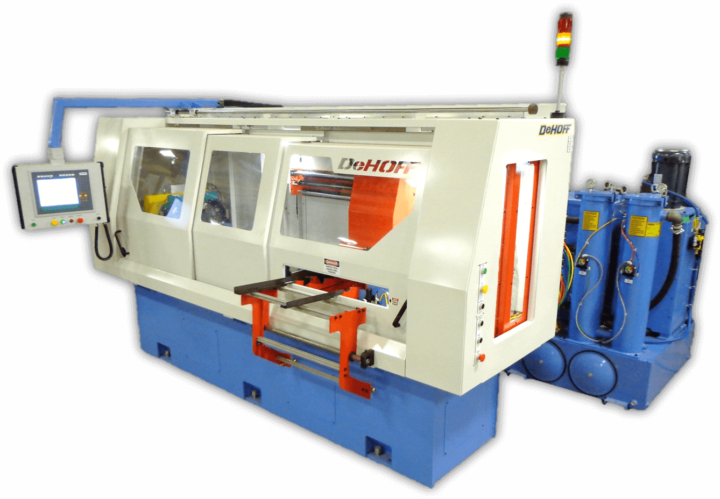